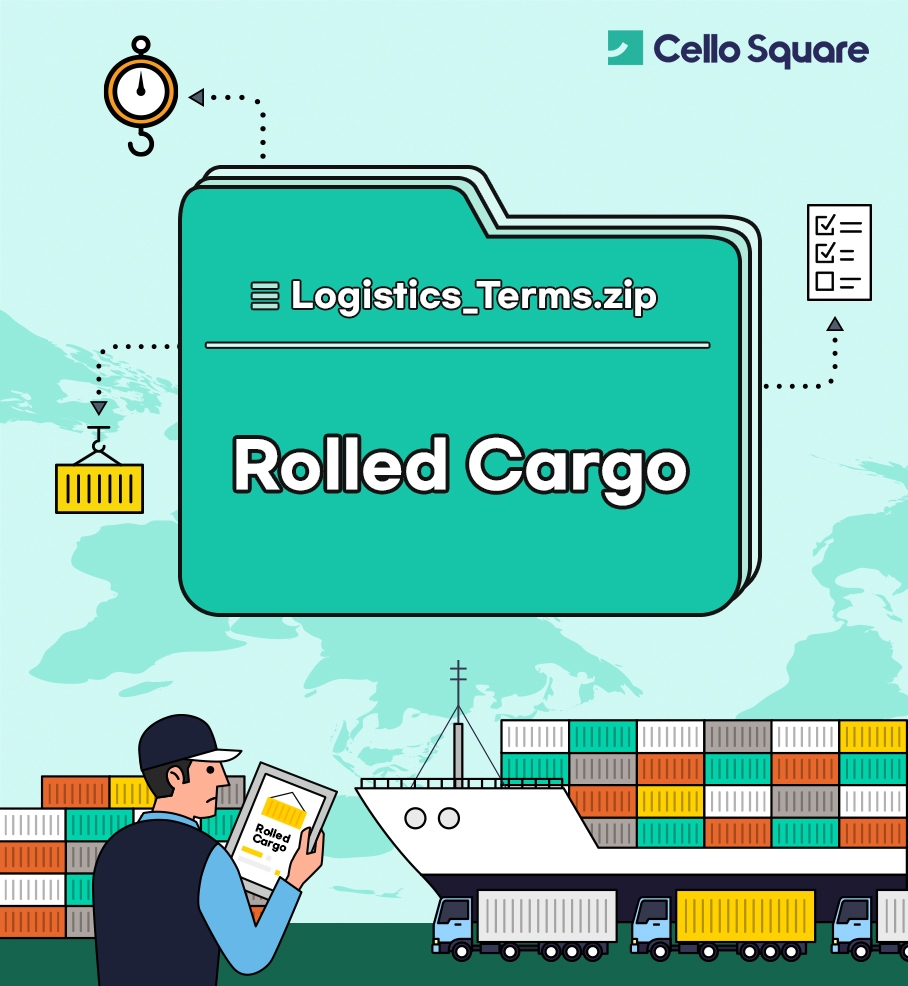
Rolled cargo refers to goods that were unable to be loaded onto their scheduled vessel due to the ship reaching its full capacity. Rollovers in ocean freight are a multifaceted issue, stemming from a variety of operational challenges that disrupt the planned journey of cargo containers. These disruptions can lead to significant delays in the delivery schedule, impacting the efficiency of the global supply chain. The reasons for cargo rollovers encompass a range of logistical complications:
1. Overbooking of Cargo
Occasionally, the occurrence of rolled containers falls outside the shipper's sphere of influence, with overbooking being a prevalent cause. This scenario is akin to how commercial airlines manage seat allocations, where passengers might be removed from a flight due to excessive bookings, leading to the vessel exceeding its capacity. There exists a continual risk that cargo intended for transfer to another ship might be subjected to further delays. Especially during periods of increased demand for shipping, this issue can escalate, compounding the challenge of rectifying the situation and prolonging the duration needed for recovery.
2. Exceeding Cargo Weight Limits
Containers that surpass the vessel's maximum weight capacity are left behind to comply with safety and regulatory standards. The practice of leaving behind overweight containers is a precautionary measure to prevent potential hazards associated with overloading, such as stability issues or structural stress to the vessel. Moreover, this adherence to weight limitations ensures the safety of the crew, the cargo, and the vessel itself.
3. Vessel Schedule Disruptions
Disruptions to a vessel's planned itinerary can lead to cargo being rolled, a situation often unrelated to the specifics of the shipments themselves. Occasionally, vessels may bypass a scheduled port call due to operational decisions or constraints, resulting in containers meant for that port being rolled to the next available shipment. An ocean freight carrier might modify its sailing schedule, possibly omitting a port stop due to various factors such as adverse weather conditions. Additionally, challenges like vessel weight limitations, technical glitches, mechanical failures, or congestion at ports could further complicate the schedule.
4. Incorrect Documentation
Errors in cargo documentation can halt the loading process until the paperwork is corrected, potentially missing the vessel's departure. Such scenarios might arise from errors the shipper commits while preparing shipment paperwork. A mistake in the cargo declaration, for example, can trigger delays during customs processing. These incidents underscore the critical importance of meticulous attention to documentation well in advance of the vessel's departure date. Ensuring that all paperwork is accurate and submitted timely is essential for a smooth customs clearance process, thereby minimizing the risk of unnecessary delays and rolled cargo situations.
5. Customs Clearance Disputes
Issues arising from customs can prevent a container from being loaded onto a vessel until the dispute is resolved. Such disputes often involve discrepancies in documentation, valuation, or compliance with import/export regulations, requiring timely intervention to prevent shipping delays. These issues can halt the shipping process, keeping a container dockside until all disagreements are adequately addressed and resolved.
6. Transshipment and Lesser-known Destinations
Containers that need to be transferred across multiple vessels to reach their final destinations are particularly susceptible to being rolled. The complexity of coordinating these successive vessel transfers, especially to ports that are less commonly served, increases the likelihood of logistical hiccups. This heightened risk is attributed to the intricate scheduling and space allocation required for each leg of the journey, often compounded by limited shipping schedules to these less accessible locations. These factors together amplify the potential for delays and the subsequent rolling of cargo, emphasizing the need for precise logistical planning and coordination in the face of the inherent unpredictability of maritime transport.
7. Mechanical Problems with a Vessel
Unexpected mechanical issues can lead to the rescheduling of cargo to ensure safety and adherence to maritime regulations. These issues can range from engine failure to problems with navigation systems, all of which directly impact the vessel's ability to operate safely and efficiently. When such mechanical failures occur, the priority shifts to addressing these concerns promptly to minimize risks to the crew, cargo, and vessel. This focus on safety can lead to delays in the shipping schedule, as cargo may need to be transferred to a later voyage to accommodate necessary repairs or maintenance.
For situations like overbooking and mechanical failures, the responsibility primarily falls on the carrier, who must then reschedule the shipment without imposing additional charges on the shipper. This dynamic underscores the inherent uncertainties within ocean freight logistics and the importance of robust communication and contingency planning between shippers and carriers. By understanding the various causes of rollovers, stakeholders can better anticipate and mitigate the impacts of these disruptions on their operations.(Source: Firefly, Adobe)
When cargo gets rolled, the implications and subsequent actions largely depend on the underlying cause of the rollover. In cases where the rollover is due to carrier-related issues such as overbooking or mechanical problems with the vessel, the carrier bears the responsibility for the inconvenience. They typically take immediate action to reschedule the affected shipment, ensuring it is placed on the next available vessel departing for the intended destination. The cargo will be scheduled for the next vessel, often a week later. In such instances, any additional charges incurred due to the rescheduling are usually absorbed by the carrier, alleviating any extra financial burden on the shipper.
Conversely, if the rollover occurs because of issues on the shipper's end, such as incomplete or missing paperwork, customs clearance problems, or non-compliance with specific shipping requirements, the financial responsibility shifts to the shipper. Under these circumstances, the shipper may face charges for the rollover, which can sometimes exceed the original cost of the ocean freight. This underscores the importance of thorough documentation and compliance with all regulatory and shipping guidelines.
Delays in the supply chain, especially those resulting from container rollovers, can lead to a cascade of consequential costs, significantly impacting the overall freight invoice. While it's challenging to enumerate all possible expenses due to the variability and complexity of shipping operations, the primary charges that often surface in the wake of a rollover include:Demurrage Charges: Imposed by the shipping line for containers that remain in the port beyond the allotted free time, reflecting the cost of occupying space longer than scheduled.
Storage Fees: Levied by the port for holding the cargo beyond the designated free period, which covers the cost of utilizing port space for storage.
Detention Charges: Charged by container truckers for the use of containers outside the port beyond the agreed free time, compensating for the delayed return of containers.
Customs Inspection Fees: Incurred when cargo requires inspection by customs authorities, an event more likely if documentation irregularities or other compliance issues arise.
Customs Penalties: Applicable if any customs regulations are breached, whether due to documentation errors, misdeclaration of goods, or failure to comply with import/export standards.
In any scenario where cargo is rolled, communication plays a crucial role. Carriers are expected to notify the booking party of the rollover, providing updated booking information and new departure details if the issue is carrier-related. For those who have arranged their shipment through a freight forwarder, the freight forwarder will receive this information from the carriers and then communicate the updates to the shipper. This ensures that all parties involved are informed of the situation and any changes to the shipping plan, facilitating a smoother resolution process.
Preventing cargo from getting rolled is pivotal in maintaining the efficiency and reliability of your supply chain. While there's no foolproof method to completely eliminate the risk of your shipment being delayed, adopting certain strategies can significantly reduce this likelihood and help manage any disruptions more effectively:
1. Early Booking
Secure your shipment slot well in advance. Early booking allows ample time to gather and verify all necessary documentation, ensuring everything is in order for smooth customs clearance. This proactive approach can be particularly beneficial in avoiding last-minute hassles and potential rollovers.
2. Flexibility in Sailing Dates
Maintaining flexibility with your shipping dates can serve as a safeguard against unforeseen delays. By not locking into a single sail date, you increase your chances of finding alternative shipping options should any issues arise, thereby minimizing the impact on your overall supply chain.
3. Avoiding Peak Seasons and Major Holidays
Vessels are more likely to be overbooked during high-demand periods, such as the peak season from mid-August to mid-October, and around significant holidays like China's Chinese New Year and Golden Week. Planning shipments outside these busy times can reduce the risk of your cargo being rolled due to space limitations.
4. Minimizing Transshipments
Containers routed through transshipment points are at a significantly higher risk of experiencing rollovers. This risk applies not only at the initial port of departure but also at each transshipment port along the journey, regardless of their number or locations. Transshipments add layers of complexity to the shipping process, involving additional handling and coordination at each transfer point, which in turn increases the likelihood of delays or scheduling conflicts. By opting for direct routes whenever possible, shippers can reduce these risks, streamline their logistics, and enhance the reliability of their cargo's arrival time.
5. Splitting Your Bill of Lading (B/L)
The decision to roll cargo is often based on the Bill of Lading rather than the physical container itself. If your shipment consists of multiple containers under a single B/L, the carrier's decision to roll will apply to all containers listed under that B/L – it's an all-or-nothing scenario. A strategic workaround is to distribute your shipment across several Bills of Lading. This diversification increases the likelihood that, should any part of your shipment be rolled, other parts may still proceed as planned, thereby minimizing the overall impact on your shipment's delivery schedule.
6. Managing Documentation Requirements
Proper and meticulous management of documentation is essential in preventing shipping delays and rollovers. Ensuring that all required paperwork is completed thoroughly and accurately is crucial for a smooth customs clearance process. This includes making sure that all forms, such as the Bill of Lading, commercial invoices, packing lists, and any necessary certificates or permits, are filled out with precise and correct information. Errors or omissions in documentation can lead to hold-ups in customs, which might result in your cargo being rolled. By prioritizing the accuracy and completeness of all documentation well in advance of the shipping date, shippers can significantly reduce the risk of unexpected issues and contribute to the timely and efficient transport of their goods.
7. Partnering with a Reputable Freight Forwarder
Collaborating with a seasoned freight forwarder can significantly mitigate the risk of cargo rollovers. A freight forwarder with extensive experience and knowledge about problematic routes or ports will offer invaluable advice on avoiding such issues. They can also assist in rerouting shipments when necessary. Moreover, an established freight forwarder might possess greater leverage in negotiations with carriers, potentially securing a spot for your shipment even in cases of overbooking where your cargo faces the risk of being left behind.
By implementing these strategies, shippers can enhance the predictability and reliability of their cargo shipments, even in the dynamic and sometimes unpredictable realm of maritime logistics.(Source: Firefly, Adobe)
Shippers should also recognize the role that supply chain visibility plays in decreasing the chance of a rollover and managing the disruption when it does occur. The significance of supply chain visibility transcends mere shipment tracking; it is a pivotal strategy for mitigating the risks associated with rolled cargo. Enhanced visibility into the supply chain enables shippers to better plan and execute their logistics operations, reducing the likelihood of disruptions and managing them more effectively when they do arise. Here's how visibility plays a crucial role:
Advanced Planning for Shipments: With comprehensive visibility, shippers can accurately schedule their shipments well in advance. This foresight allows for early quote requests, ensuring that cargo is booked and prepared for shipping well before the required departure date. Early planning is particularly crucial during ocean freight's peak seasons, where the risk of rollovers is significantly higher.
Preventative Measures During Peak Seasons: Visibility into the supply chain offers valuable insights that help shippers anticipate and prepare for peak shipping periods. By understanding when these high-demand times occur, shippers can implement strategies to mitigate the risk of rollovers, such as booking extra capacity or choosing less congested routes.
Proactive Response to Milestone Events: Real-time visibility into container movements and milestone events allows shippers to proactively address potential disruptions. For instance, if visibility tools indicate port congestion, shippers can interpret this as a sign of tight capacity and may decide to secure their shipping arrangements sooner rather than later to avoid rollovers.
Reevaluation of Booking and Documentation Processes: Rollovers resulting from booking or documentation errors highlight the need for shippers to reassess their operational processes. Visibility into these aspects of shipping can reveal patterns or recurrent issues, prompting shippers to refine their approach to documentation and booking practices, thereby reducing the risk of future rollovers.
In essence, supply chain visibility empowers shippers with the data and insights needed to make informed decisions, anticipate potential challenges, and adjust their strategies accordingly. This level of oversight and control is invaluable for maintaining the fluidity of the supply chain, minimizing the financial and operational impacts of rolled cargo, and ensuring the timely delivery of goods.
-
In conclusion, while the occurrence of rolled cargo in the maritime logistics industry presents a complex challenge, understanding its causes and implementing strategic measures can significantly mitigate its impact. Early booking, flexibility in sailing dates and working with reputable freight forwarders are effective strategies that shippers can employ to reduce the likelihood of experiencing rolled cargo. Additionally, the importance of supply chain visibility cannot be overstated, as it equips shippers with the necessary insights to plan proactively, respond to potential disruptions, and refine their shipping practices. By adopting these approaches, shippers can enhance the resilience of their supply chain operations, ensuring smoother, more reliable delivery of cargo despite the dynamic and sometimes unpredictable nature of global shipping logistics.